
How
to create an elastic boundary element
The elastic spring
is used as a ground boundary condition for
Eigen value analysis and Response spectrum
analysis.
Creating
an elastic spring can be hard for beginners
and the elastic spring element can be created
from the following steps.
1.Use
the elastic modulus of the ground to compute Kv0. (The Equation
is shown below.)

Here,
E0: Elastic modulus of the ground, a Coefficient
depending on test condition
Modulus
of deformation E0 from the following test
methods (kfg/cm2) |
a |
Regular time |
During
earthquake |
1/2
of E0 from the cyclic curve of the plate
load test, d1 using a rigid circular plate
of 30cm diameter |
1 |
2 |
E0
measured in the borehole |
4 |
8 |
E0
from the unconfined or tri-axial compression
test on a specimen |
4 |
8 |
E0 estimated by
the N value from the Standard Penetration
test when E0=28N |
1 |
2 |
2.
Re-calculate the Subgrade Reaction Modulus Kv(=
Kh) using the computed Kv0.
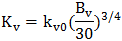
Here,

The
area Av becomes the area where the subgrade reaction
spring will be installed.
If the model exists like
the following figure,
Area
of Ground A is Av=1m(Left length of model)*1m(Unit
width of 2D analysis)=1m2, Bv becomes 1m=100cm.
Using
the same method, the unit width of Ground B is
Bv=√(20000)cm=141.42136 cm.
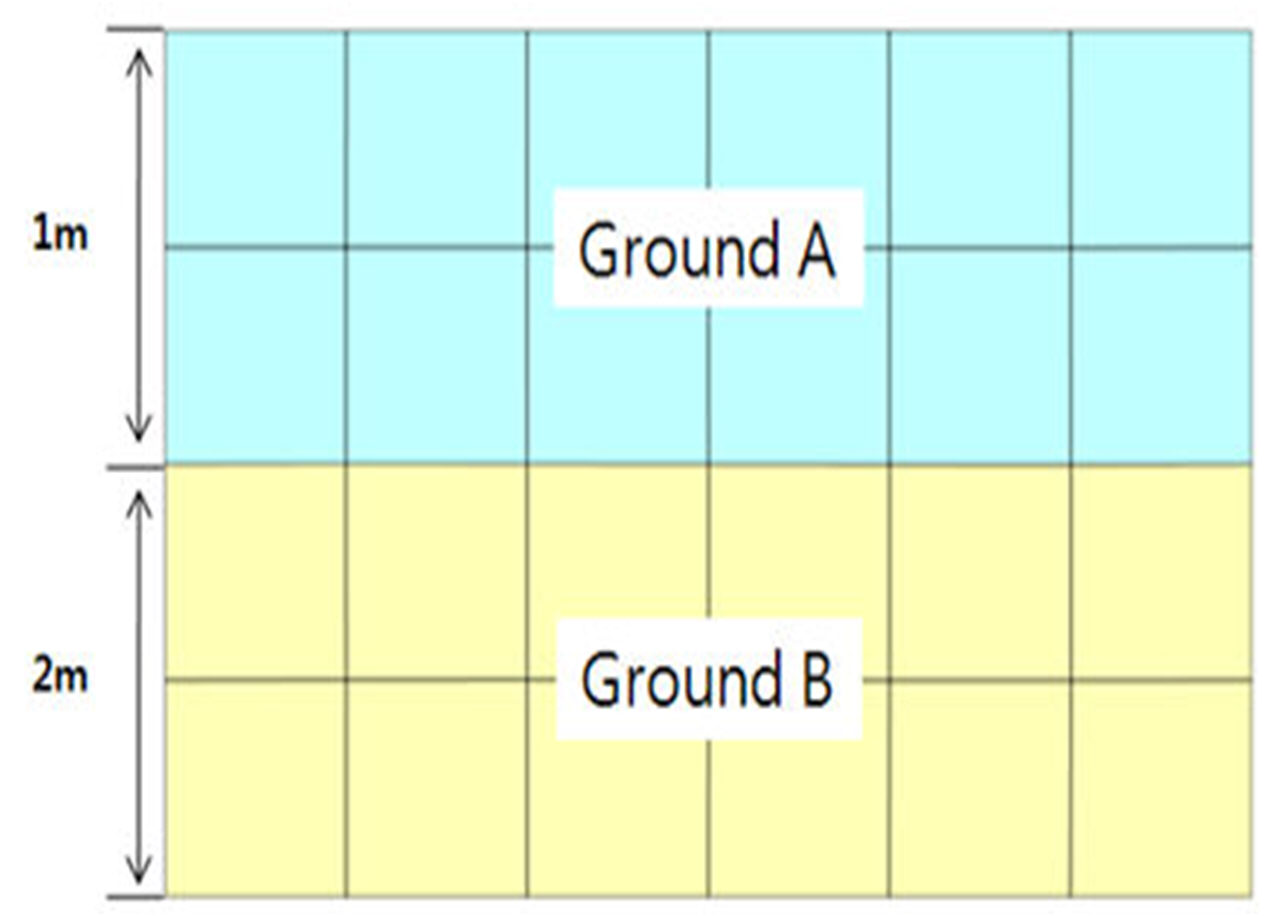
Ultimately,
the Subgrade Reaction Modulus K can be computed
and a point spring is created on the node, considering
the area of the element.
|
E
(tonf/m2) |
Ky0 |
A
(cm) |
B |
K
(tonf/m3) |
α |
Ground
A |
1000 |
3.3333 |
1.00E
+ 04 |
100 |
1351.186643 |
1 |
Ground
B |
2000 |
6.6667 |
2.00E
+ 04 |
1414213562 |
2083.845925 |
1 |
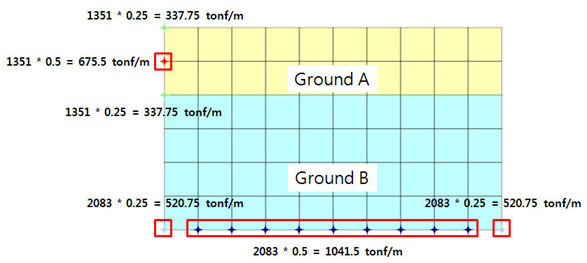
The spring coefficient
of the floor (Z direction) is created with the
same value as the X direction.
(Element
length x Width (1m) = Cross sectional area, so
only consider the effective length of the element.)
2
overlapping boundary elements are created where
the ground and ground meet.
How
to create a viscous boundary element
1.
Compute Cp, Cs
Cp,
Cs can be calculated using the equation below.

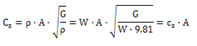
Here,
, ,
λ
: Bulk modulus, G : Shear modulus, E : Elastic
modulus, ν : Poisson’s ratio, A : Cross-section
area
2.
The cross-section area is automatically considered
until the surface spring is created, so only the
Cp, Cs needs to be computed.
|
Elastic
modulus |
Bulk
modulus |
Shear
modulus |
Unit
weight |
Poisson’s ratio |
P wave |
S
wave |
|
E
(tonf/m2) |
λ
(tonf/m2) |
G
(tonf/m2) |
W
(tonf/m3) |
ν |
Cp
(tonf·sec/m3) |
Cp
(tonf·sec/m3) |
GroundA |
1000 |
864.1975309 |
370.3703704 |
1.8 |
0.35 |
17.1605 |
8.2437 |
GroundB |
2000 |
1459.531181 |
751.8796992 |
2 |
0.33 |
24.5792 |
12.381 |
Multiplying the Cp, Cs
(tonf•sec/m3 units) to the cross-section area
eventually leads to the spring stiffness of the
viscous boundary element in tonf•sec/m units.
The
shaded cell parameters are the physical properties
of the ground the user inputs during modeling
and the Bulk modulus and Shear modulus are calculated
using the Elastic modulus and Poisson’s ratio.
Hence, there is no need to input additional values
when creating a viscous boundary element.
When
creating the viscous boundary element automatically,
the spring is automatically created by considering
the element area (effective length*unit width)
as shown below. Input the Cp value for the normal
direction coefficient at the point of spring creation
and input the Cs value for the parallel direction.
For
example, the Cx of the spring coefficient created
on the left/right of the model is the Cp of each
ground and Cz becomes the Cs value. The bottom
spring coefficient Cz becomes the Cp value.
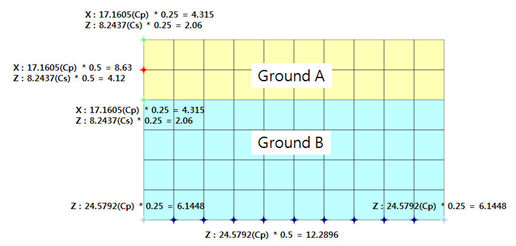

|